Precision agriculture in Israel, invented the sweet pepper picking robot Sweeper
Rest assured that robots will not be able to occupy our world in the short term, because even the most basic operational tasks will leave them at a loss as to what to do. Have you ever thought about how difficult it would be to let a robot pick a mature bell pepper by itself?
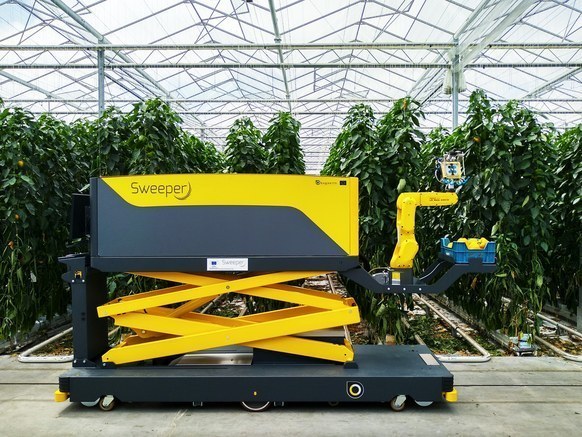
To be honest, I haven't thought about it either, but it's clear that researchers from Israel and Europe have been studying it for a long time. They are currently developing a robot called Sweeper, which can patrol around the greenhouse where sweet peppers are grown to see if they are ripe and pick them off and put them in baskets.
In fact, we can think of the Sweeper as a self-driving car, but this "car" has a sawtooth in the front and its destination is pepper plants. In the greenhouse, Sweeper uses sensors such as lidar (to determine the distance by firing a laser beam) to determine its own path, and during its tour along the plant path, it stops to photograph the target image every few feet.
"when Sweeper finds a chili-like target, it tries to get close to it," said Polina Kurtser, an industrial engineer at Ben Gurion University in Israel. " And will make a more detailed observation of the target object, stretching the head back and forth (equipped with the camera) to view the target object from multiple angles. In the process, Sweeper itself casts light on the plant, meaning it works well in the greenhouse, day or night.
By projecting light onto the target object, Sweeper can observe the color of the sweet pepper more carefully to confirm its maturity. Because if the sweet pepper is in the right state, the color on the surface of the sweet pepper will show an uneven change, some areas will turn yellow, and there will be green patches in addition. In this state, sweet peppers are not fully mature, but this is exactly what Sweeper is looking for, because in the process of picking and entering the market, sweet peppers will continue to mature to consumer satisfaction.
Then comes the most critical picking process: Sweeper positions the head to make sure the serrated eyebrows are right above the stem of the pepper plant, and the shovel spoon on the robot's chin is under the sweet pepper fruit. In this way, after being sawtooth, the sweet pepper will fall directly into the shovel spoon, turn and eventually enter the collection blue basket.
The whole process takes 24 seconds, Kurtser said. "at the moment, you may think that 24 seconds is too long, because human workers may be able to do it in three to four seconds. But don't forget that human workers can't work 24 hours a day. " And now the researchers are running the machine in a slow mode, mainly for safety reasons, and they think it is possible to reduce the picking time to 15 seconds, considering the safety of the people working around the machine.
In this process of picking sweet peppers, one of the biggest obstacles is precisely in the simplest operation: it takes 3 to 4 seconds to put the sweet pepper into the fruit collection basket, because it must turn the sweet pepper away from the direction of the plant and then carefully put it into the basket. To achieve a picking time of 15 seconds, they may use some kind of pipe that allows the sweet pepper to reach the basket directly after being cut, omitting the shovel transfer step in the middle.
In fact, it is not easy for Sweeper to achieve what it is now. Because we all know that the greenhouse where plants grow is hot and humid, which is not friendly to robot sensors at all, and engineers have to order special boxes and materials to make the sensors work in this environment. "We humans don't like working in high-calorie environments like greenhouses, and neither do sensors," Kurtser said.
In addition, Sweeper faces a challenge: the interior of the greenhouse is not the well-organized structural environment that is usually suitable for robots to work. Although the plants are arranged neatly and orderly, the gap is very small, and the plants are spread all over the greenhouse space. "if you want to run a robot in a BMW workshop, you can create an environment conducive to its operation," Kurtser explained. But to run robots in this agricultural environment, you really can't design too much, and you have to adapt to the environment there. "
Admittedly, different crops require different types of robots, so you can't just put the Sweeper in an apple orchard and expect it to bring you back a basket of apples. But this does not mean that the design ideas and ideas of this robot can not be used by other similar crop picking robots. The researchers say that after a slight adjustment to the Sweeper, it can be used to pick cucumbers.
"[sweet pepper and cucumber picking robots] face the same problems in terms of barriers, density and planting systems," Kurtser said. A major difference is that the criteria for identifying cucumber maturity are different from those for sweet peppers. "therefore, there are some things you can use directly, but you need to design another algorithm to detect maturity."
Different crops have different requirements for robot picking and placement. "delicate fruits like strawberries need to be picked and put directly into the final container to prevent friction damage, while vegetables such as sweet peppers can go through an intermediate step like bulk packing," said co-founder and CEO Brandon Alexander of Iron Ox, which is developing a robot that works in a greenhouse environment.
Sweeper and other varieties of picking robots are only just beginning to take shape. But judging from the 20% labor shortage on California farms, now is a good time for robots to enter the farm.
- Prev
Modern Farmer, a foreign agricultural magazine, has been turned into a fashion magazine
Hello, honey, is it convenient to talk? Well, there is a very good chicken in our family recently, which is in line with the position of your magazine! I just want to say, can we give it an exclusive interview? Or make a blockbuster? I'd like to ask about the specialty of this kind of chicken that we usually have to make.
- Next
Practical cultivation techniques of Lentinus edodes and new techniques for fast-growing and high-yield cultivation of Lentinus edodes
Lentinus edodes, known as Lentinus edodes, is a low-calorie food. If you eat 50 grams of Lentinus edodes a day, you have only 15 calories. Eggs are also high in self-quality and fiber, and rich in calcium. In addition, Lentinus edodes also contains two ingredients that have been proved to be effective, namely incense.
Related
- A one-day flower show brings 130 million yuan in orders! Nanhai, this Phalaenopsis exhibition is amazing
- What do the flower language and meaning of Lutheran tree mean? Precautions for planting Lutheran tree
- Encounter Chaoshan Kongfu tea, not without this cup of Phoenix single clump
- The durian market in Vietnam and Thailand is flooded. The price of imported durian has plummeted by 30-40% in a month.
- Shanghai solved the problem of local vegetable supply by planting 80,000 mu of green leafy vegetables.
- Wageningen University has become the best agricultural university in the world for the seventh time in a row.
- The strongest export season of South African grapes is full of challenges, with exports to Russia falling sharply by 21%.
- Sri Lanka is on the verge of bankruptcy, "Tea for debt" Organic Agriculture Revolution aggravates the Food crisis?
- Turning waste into earthworm manure and worm manure into organic fertilizer-A new choice for auxiliary farming
- Organic rice growers shoulder the responsibility of nurturing agricultural talents! Yinchuan Sustainable Farm with Organic Life Camp